AH-64メイン・ローター・ストラップ・パックの改修
「メガ・ナット」ストラップ・パックへの改修およびフェイル・セーフ・カラーの取付
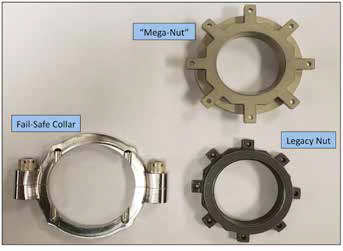
2年前にアパッチで発生したある死亡事故の原因は、調査の結果、メイン・ローター・ストラップ・パックのアウトボード・ナットのクラックであったことが判明した。そのクラックは、応力腐食割れにより生じたものであった。
この問題により、アパッチが飛行停止になることはなかったが、そうなってもおかしくない状況であった。クラック発生によるリスクを低減するため、ボアスコープ点検の頻度が増加された。その点検自体は部隊にとって特別なことではなかったものの、即応性の低下をもたらしていた。
それから20か月の間、航空企業およびその関連組織は、新型ストラップ・パックの設計、製造および供給に努力を傾注し、陸軍のリスクと陸軍兵士の負担の軽減に寄与してきた。今月、9番目の飛行大隊における改修作業を開始するにあたって、この問題を解決するために行われてきた過去に例を見ない業務の一部を紹介することとしたい。
一般的に、すでに使用されているヘリコプターの構成部品を再設計することは、簡単ではない。今回の再設計も、例外ではなかった。ストラップ・パック再設計チームには、アパッチ・プロジェクト・オフィス、航空設計部局、AMCOM(U.S. Army Aviation and Missile Command, 航空およびミサイル・コマンド)兵站センターおよび国防契約管理局からの代表者たちが参加した。その業務は、アパッチの製造会社であるボーイング社およびその下請け会社と連携しつつ実施された。
すべての関係者は、AMCOM司令官のダグ・ガブラム少将が議長を務めるミーティングに毎週参加した。チームの要であったガブラム司令官および航空プログラム・エクゼクティブ・オフィサーのトーマス・トッド准将は、取り組むべき問題に焦点を集中し、この対策の実施に伴うリスクと負担を可能な限り迅速かつ確実に低減することに努めた。
アパッチにおけるこの問題に対する解決策は、MNSP(“mega-nut” strap pack, メガ・ナット・ストラップ・パック)と呼ばれている。新しいストラップ・パック・ナットは、より大きな断面積を有する新たな形状に再設計され、応力負荷を軽減するとともに、より耐久性および耐腐食性のある材料を用いている。
どの部隊に、FSC(fail-safe collar, フェイル・セーフ・カラー)またはMNSPのどちらを適用するか、という優先順位は、陸軍省命令執行部(The Department of the Army Execution Order, DA EXORD)により決定された。優先的に改修が進められることになったのは、沿岸部に駐屯している9つの部隊であった。すべてのAH-64保有部隊を対象に改修を進めたいところではあったが、ボーイング社およびAMCOMから派遣されるチームによるMNSPへの改修を完了するには、相当な期間が必要と見積もられた。このため、従来の部品にかぶせるように取り付けて冗長性を確保し、当面の安全性を確保するように提案されたのがFSCであった。FSCを取り付けることにより、MNSPを用いた改修が逐次実施される間の陸軍全体のリスクを軽減できるのであった。
私は、FSCおよびMNSPの双方について、部隊での改修作業に立ち会ってきた。軍の整備員、企業の技術派遣要員、またはその両方で構成された改修チームは、この3か月間、晴らしい成果をもたらしてくれた。以下、その一部を紹介することとしたい。
MNSP(Mega-Nut Strap Pack, メガ・ナット・ストラップ・パック)
MNSPへの改修作業は、P4T3(Problem, People, Parts, Plan, Time, Tools, & Training, 目標、人、部品、時間、工具および訓練)、協力およびチームワークの実践の場であった。この任務を完遂するためには、部隊の兵士たちとボーイング・チームの協力が不可欠であるが、これまでのところ、順調に進んでいる。改修作業は、部隊が機体を準備し、ボーイング・チームがストラップ・パックの改修を実施したのち、部隊が復旧および飛行試験を実施する、という分担で行われた。部隊とボーイング・チームのそれぞれの地位と役割を明確に区分することにより、それぞれのチームが迅速に作業を行えただけでなく、それぞれの任務に集中することにより、品質管理の徹底を図ることができた。
陸軍省命令執行部の計画は、1日あたり4機を改修するように定めていたが、部隊が必要な支援を行うことによって改修機数を増加することも容認していた。このため、最近の改修作業においては、1夜で9機の改修を行った場合もあった。
慎重であること。品質を維持すること。手を抜かないこと。他の整備作業と同様に、運用と整備のバランスを適切に維持するとともに、決して拙速にならないように着意された。
同時に、あくまで部隊の意思が尊重された。業務の継続性を考慮して計画されていたものの、柔軟性の維持に努め、改修の加速を追求した。また、部隊のMNSP改修およびその関連業務に対する満足度を把握するため、ガブラム少将およびトッド准将は、それぞれの部隊長を通じて各部隊の実施状況を確認した。
FSC(Fail-Safe Collar, フェイル・セーフ・カラー)
FSC(フェイル・セーフ・カラー)の取り付けは、ストラップ・パックの改修よりも作業が容易であるため、少人数のチームをもって実施が可能である。カラーの取り付けに要する時間は、2名の整備員で、約2時間半であった。当初は、作業が容易なことから、すべての機体に直ちにカラーを取り付けることが考えられていた。つまり、FSCは暫定処置として考えられていたのである。しかし、その場合、部隊は、その後のMNSP改修の際に再びローター・ヘッドを分解しなければならなくなる。それは、必要な部品が2倍となり、非可動時間が2倍となり、整備員の負担が2倍になることを意味する。このため、行動方針が変更され、関連する計画整備を実施する機体および諸職種連合訓練センターでの訓練などの主要訓練への参加が予定されている機体に対してのみFSCの取り付けを行うことになった。
この記事を執筆している時点では、約25%のアパッチについてMNSPへの改修が完了しており、FSC取り付けの対象となるすべての部隊に対し、PBL(Performance-based logistics, 装備品等の維持・整備業務を民間委託する手法のひとつ)の系統を通じて、必要なFSCの供給を完了している。
2つの改修のいずれにおいても、それを適切に完了するための鍵は、チームワークである。この困難な長い道のりを乗り越え、部隊における機体の信頼性と即応性を回復し整備上の負担を軽減するため、航空企業は、多大の貢献をしてくれている。ボーイング社などの航空関連企業の協力がなければ、現在、我々が行っている業務は、間違いなく、数か月以上遅れていたことであろう。
本件は、部隊の整備員を支援するため、企業の技術派遣要員を適切な時期および場所にいかにして派遣すべきかを決定するうえで、非常に参考となる事例であった。最後に、企業と軍隊は同じチームの一員である。背番号は違うかもしれないが、同じ緑色のユニフォームを着ているのだ。
上級准尉5 マイケル・D・カバコは、アラバマ州レッドストーン工廠の航空およびミサイル・ライフサイクル管理コマンドの航空部局整備幹部です。
出典:ARMY AVIATION, October 2018, Army Aviation Association of America 2018年10月
翻訳:影本賢治, アビエーション・アセット管理人
備考:本記事の翻訳・掲載については、出典元の承認を得ています。
アクセス回数:4,834
管理人 へ返信する コメントをキャンセル
2件のコメント
「ストラップ・パックとメガ・ナットおよびアウトボード・ボルトの位置関係」や「ストラップ・パックの改修が全体的なものなのか、メガ・ナットだけなのか」が原文だけでははっきりとしません。「アウトボード・ボルトとメガ・ナットで、ストラップ・パックを挟み込むように取り付けられている」、「改修されたのは、ストラップ・パックの構成品であるメガ・ナットのみ」と解釈して翻訳しています。
誤りがあれば、教えてください。
本改修実施の発端となった死亡事故に関するFlightfaxの記事をこちらに掲載しました。